What We Do
Our Services
Quality Services
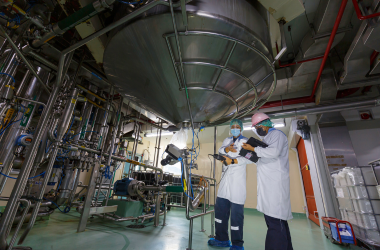
Distributing of Ultrasonic processing equipmentinning
Our company supplies a range of industries with commercial Ultrasonic processors
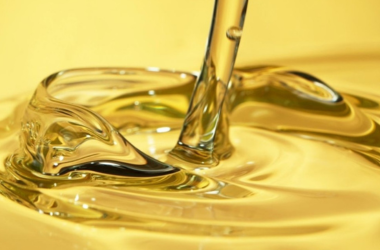
Lubricating Oils
Major benefits of Ultrasonic Technology for Lube Oil Blending Environmental benefits through energy savings Financial benefits through lower operating and maintenance costs Increased operational efficiency Very low carbon foot print 10 tonnes or ten thousand of lube oil can be manufactured in one hour using 3kw tubular processor without heat, agitation or moving parts Using the Ultrasonic method eliminates production delays arising from heating, cooling and mixing high quality 24/7 One vessel for blending and discharge to filling facilities Download our presentation for more information Find out more Download a PDF version of our presentation for further information about the technology DOWNLOAD For further information or for full no obligation, no cost presentation at a venue of your choice, please get in touch
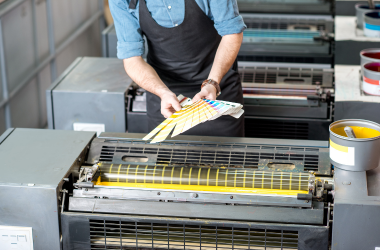
Manufacture and Recycling of Paints
This system uses an ultrasonic tubular processor that is based on sono-chemical and ultrasonic principles. High-speed interparticle collisions brought on by ultrasound waves are utilized in the ultrasonic paint manufacturing process to accomplish task including deagglomeration, de-gassing, milling, mixing and emulsification. This achieves several advantages that are outlined below and does away with the need for mechanical ball and micro milling techniques. Enhanced productivity and effectiveness. During testing and currently in production, the ultrasonic processor requires 32 minutes to produce 1 tonne of paint. Thus utilizing around 1/12th of the prior amount of energy needed per hour, production is achieved in 1/16th of the regular production time (i.e., 6-8 hours using a basket mill) Benefit to the environment from energy savings. Since producing ultrasonic paint require very little energy, the amount of emissions produces is greatly reduced. This is also true for paint recovery from production waste using ultrasonic technology, as disposing of paint waste results in much lower solvent emissions. Operators are thus exposed to far less VOC, anf their carbon foot print is reduced. Financial gain made possible by: lower operational expenses due to fewer time and power requirements (one of our clients has been using a 1.5KW processor for all their white based manufacturing for the past 12 months for example). Apart from the benefit of being free of moving parts, the tubular processor’s ultrasonic characteristics also reduce the amount of cleaning media needed for production line circuits, allowing for faster and simpler cleanups than would otherwise be possible with traditional basket mills. This facilitates seamless transition between product lines using the same machinery Contact us to Know more about this technology